How the Metaverse Can Help Manufacturers
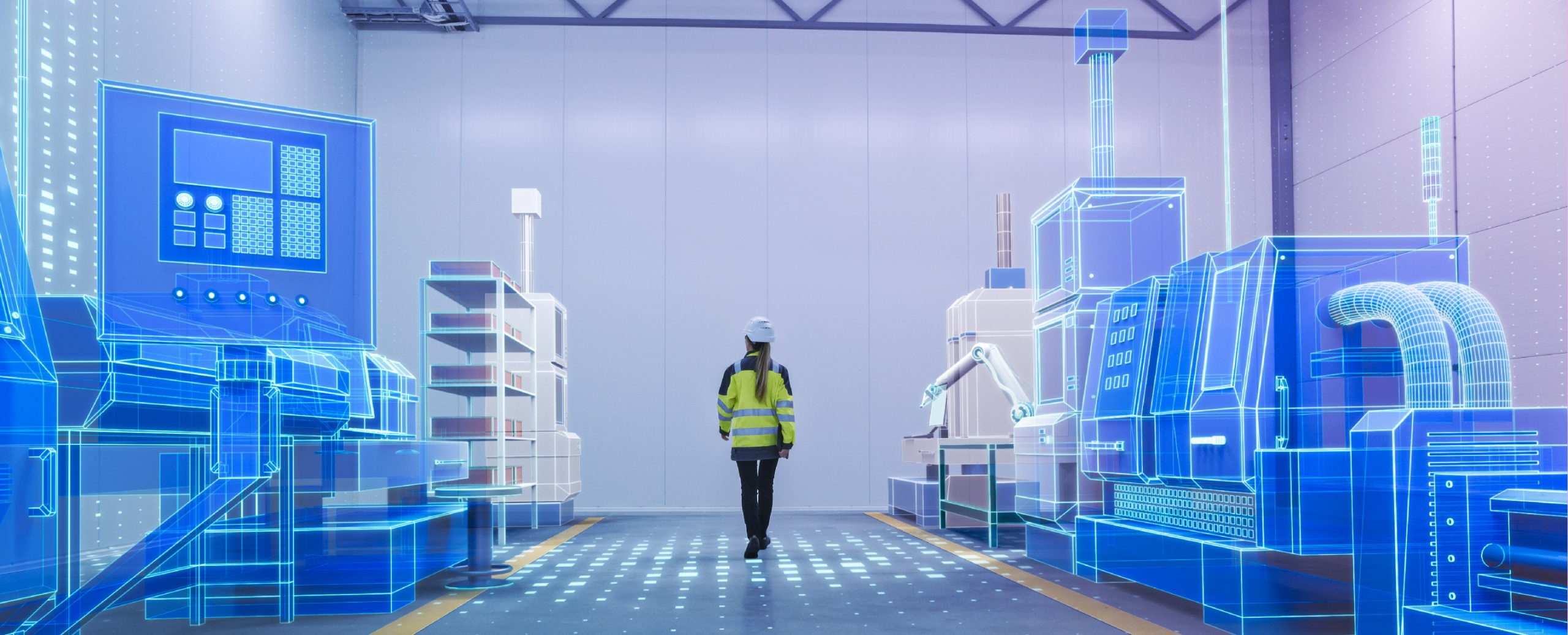
Much of the conversation about the metaverse today revolves around its essential building blocks such as NFTs, digital currencies, and enabling technologies. And that conversation is important because the metaverse needs a reliable foundation to take hold.
But the metaverse needs to prove its value industry by industry to achieve real adoption. When more corporations see how the metaverse can solve business problems, they will invest into this emerging world, and this corporate investment is essential. Businesses have the scale and budgets needed for the metaverse to achieve critical mass.
Let’s take a closer look at how the metaverse can deliver value in one industry: manufacturing.
A Quick Refresher: What Is the Metaverse?
The metaverse is a virtual world in which people interact through digital twins known as avatars in immersive environments, as we discuss in a recently published white paper from Centific, The Metaverse: A New Horizon in Digital Reality. Those environments might use extended reality technologies such as virtual reality (VR), augmented reality (AR), and mixed reality (MR).
Businesses such as fashion brands are creating virtual products for sale in metaverse environments such as gaming platform Roblox. In May 2021, Gucci and Roblox collaborated to create a virtual Gucci Garden, where Gucci sold virtual goods via Roblox currency (Robux). Gucci limited edition bags sold for the equivalent of $4,115. Meanwhile, gaming platform Minecraft has collaborated with brands such as Disney to offer virtual experiences available for a fee to Minecraft players.
Depending on whom you ask, the metaverse exists already. Indeed, aspects of the metaverse exist today; however, they are not yet connected, which metaverse purists believe needs to happen for the metaverse to exist truly.
The Metaverse and Manufacturing
Manufacturing is a critical part of supply chain management and involves many complex processes. Several components involved in the manufacturing production process include inventory costs, labor cost, speed of production, QC & QA, etc. The major pain points of this industry are quality control concerns, long-term contracts, and production design risks, which can lead to manufacturing delays, faulty products, and customer dissatisfaction.
A metaverse-driven approach in the manufacturing sector enhances the effectiveness of supply chain management, production designs, and inventory management. The three key highlights of the metaverse in manufacturing include rapid production process with collaborative product development, increase in product designs, and visibility into supply chain processes providing transparency to customers.
For example, companies are using virtual platforms that offer real-time photorealistic simulation and collaboration. This offers projects teams with the flexibility to connect at every phase of the process from ideation and conceptual design to production automation on the factory floor.
Digital Twins in Manufacturing
A digital twin can refer to a replica of a person (an avatar, as noted above), an object (such as a machine) or a place, such as the manufacturing floor. Why would a company create a digital twin of a manufacturing floor? For the same reason architects create models of structures before they build them: for safety and cost effectiveness.
Developing 3D content in real-time and assisting in the development of various applications is helpful in the manufacturing industry. Companies can use virtual copies of plants and workshops that can assist in identifying design flaws. As a result, this helps players in the manufacturing industry to efficiently design and maintain the production process.
For example, let’s say a manufacturer wants to test the efficacy and safety of a new piece of equipment outfitted with sensors before actually installing it. Any machine on the manufacturing floor is, of course, complex, with myriad moving parts such an electric motor and a driveshaft and sensors including a vibration sensor, temperature sensor, and RPM meter. Now, the manufacturer could build a digital twin that is fed real-time data from all these sensors. From there, the digital twin could provide value in many ways, such as:
- Real-time observation. A trigger programmed into the digital twin could notify maintenance personnel if the vibration level, temperature, or RPMs exceed a specific threshold. The personnel could make a course correction to prevent damage from happening.
- Historical data. Let’s say a crucial part of the digital twin breaks, such as a motor stopping suddenly. Maintenance tech could review data from the digital twin to diagnose the root cause. For example, did RPMs spike and create a temperature surge that triggered the motor breaking down? Thanks to the digital twin, this analysis could be done without the real manufacturing plant being disrupted.
- Preventive maintenance. Maintenance techs could integrate the performance data from the digital twin into the digital twin data with a computerized maintenance management system (CMMS) platform.
This is just one example. Digital twins have many more applications, such as supply chain management, where they can help businesses figure out how to get products to customers in a timelier fashion. For instance, a digital twin can predict disruptions down the line and suggest what to do about them.
Of course, a supply chain consists of interconnected businesses and functions that need to work in synch for the flow of goods to happen reliably. And we all know this has not been happening since COVID-19 laid bare the just how fragile supply chains are. One of the biggest problems in the supply chain world is a lack of visibility into data that makes it possible to forecast problems.
A digital twin can help a manufacturer by simulating conditions with real data ranging from the location of ships to the speed with are being loaded at docks. With that data, a manufacturer can do scenario planning. A very practical example consists of doing stress tests in the supply chain. For instance, a manufacturer considering the sourcing of microchips in Taiwan could test the likelihood of a drought happening in Taiwan and the resulting impact on microchip production. Or a car manufacturer assessing whether it wants to switch parts suppliers from Idaho to California could assess potential risks and threats to the supply chain resulting.
Benefits
Digital twins can deliver myriad benefits to manufacturers. On the plant floor alone, benefits include:
- Reduced waste. More insight into machine operations means reducing total. machine waste.
- Improved throughput. The ability to keep a machine up and running at peak efficiency improves the total throughput of a line.
- Better uptime. Stronger insight into equipment function and potential catalysts for failure makes it possible for personnel to keep machines humming..
- Equipment longevity. Better-maintained equipment lasts longer.
- Preventive maintenance. Manufacturers with predictive data can stop problems before the happen.
- Better asset ROI. Fewer problems and longer lifespan establish a better ROI for equipment.
How to Get Started
We suggest that manufacturers first identify a specific problem they are trying to solve, such as:
- How do we get products through our supply chain faster?
- How do we make the manufacturing floor safer and more efficient?
- How can we reduce the costs associated with equipment maintenance?
And then use test-and-learn tools such as design sprints to test how a digital might help them. The beauty of the design sprint it is engineered to help a manufacturer tackle questions for which there are no obvious answers, which is ideal for the metaverse.
At Centific, we help businesses figure out how to innovate with product development cost-effectively through our own FUEL methodology, which combines tools such as design sprints with product development approaches such as lean innovation.
Contact us to get started. And read our recently published white paper, The Metaverse: A New Horizon in Digital Reality, to get a taste of our thinking on this topic.